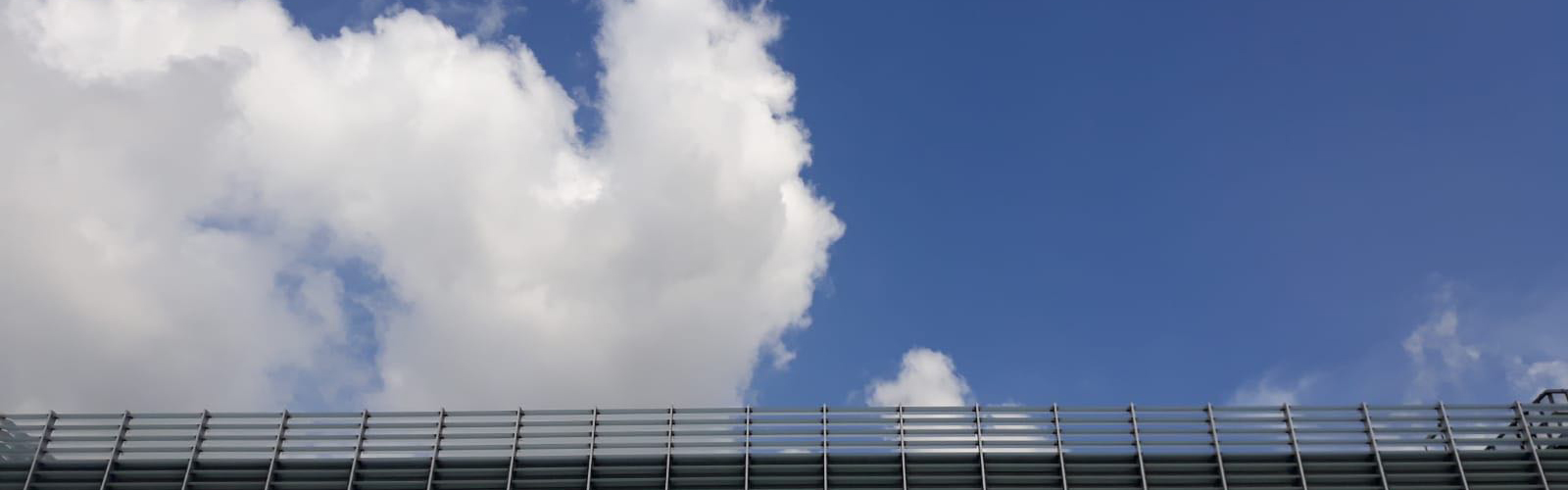
Il Current Collection Test Bench (CCTB) del PoliMi
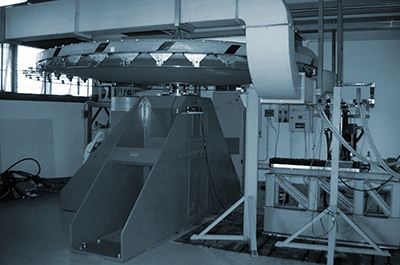
Il banco prova per lo studio del contatto tra strisciante e filo di contatto (o in inglese, CCTB, current collection test bench) è parte delle attrezzature del laboratorio di ingegneria ferroviaria e permette di provare striscianti per pantografi di dimensione reale fino a una velocità di 220 km/h, assorbimento di corrente elettrica fino a 1000 A cc ( corrente continua) estendibile in alcuni casi particolari a 1400 A cc e fino 500 A ca (corrente alternata) a 162/3 Hz, oppure a 350 A ca a 50 Hz. Il banco prova permette, quindi, di ricreare le condizioni di alimentazione elettrica tipiche della rete ferroviaria europea.
Le prove che tipicamente vengono eseguite al banco hanno l’obiettivo di valutare le prestazioni in termini di resistenza all’usura degli striscianti in funzione dei principali parametri di esercizio (velocità del treno, corrente elettrica al contatto e precarico statico o media della forza di contatto tra strisciante e filo di contatto). In particolare, è possibile eseguire prove accreditate ISO 17025:2017 (Accredia) secondo le specifiche tecniche RFI-DMA-IM.LA\ST TE65. Lo scopo di queste prove è identificare il coefficiente di attrito tra strisciante e filo di contatto e quantificare il livello di usura sia dello strisciante sia del filo di contatto.
Relativamente alle attività di ricerca il banco viene utilizzato per accrescere la conoscenza sui fenomeni elettro-meccanici e termici che caratterizzano la captazione di corrente e, più in generale, l’interazione tra lo strisciante e il filo di contatto.
Il banco è composto da due aree: una camera protetta (bunker), con una finestra con un sistema di protezione che permette l’osservazione diretta della prova, all’interno della quale si trova la parte meccanica; una parte esterna dove si trovano i sistemi di controllo e di acquisizione dei segnali.
Le parti principali del banco sono (Fig. 1):
- Un disco in fibra di vetro di 2 m di raggio che ruota introno ad un asse verticale a cui è connesso lungo tutto il perimento un filo di contatto sorretto da 36 supporti (figura 2a). Lo strisciante è montato su due sospensioni vincolate ad una piattaforma che si muove in direzione radiale rispetto al disco in modo da riprodurre il movimento a zig-zag generato dalla poligonazione del filo di contatto. La piattaforma è movimentata da un motore elettrico brushless opportunamente comandato. La somma della velocità periferica del disco, che simula la velocità del treno, e quella del moto radiale imposto allo strisciante (poligonazione) fornisce come risultato la velocità di strisciamento totale tra lo strisciante e il filo di contatto;
- Un apparato di ventilazione, che convoglia un flusso d’aria alla stessa velocità imposta al disco direttamente nella zona di contatto, al fine di riprodurre l’effetto termico del flusso d’aria che investe lo strisciante durante la marcia del treno.
La forza di contatto tra lo strisciante e il filo di contatto è applicata per mezzo di un attuatore idraulico installato sulla piattaforma mobile (Fig.2b). L’apparato di ventilazione è essenziale per riprodurre le condizioni termiche nell’area di contatto che hanno un importante effetto sulle prestazioni in termine di usura dello strisciante.
Il sistema di misura installato prevede sensori per misurare la velocità periferica della ruota ovvero del filo di contatto, la forza di contatto verticale e longitudinale tra filo e strisciante, la corrente elettrica e la tensione al contatto (Fig.3). Quest’ultimo valore viene usato per stimare la presenza di archi elettrici e, conseguentemente, identificare un indice di perdita associato all’insorgere degli archi stessi.
Il tasso di usura dello strisciante viene stimato in base alla differenza di massa dello strisciante stesso prima dell’inizio e alla fine della prova, mentre il tasso di usura del filo di contatto è ottenuto considerando la differenza di spessore del filo. La massa dello strisciante è misurata tramite una bilancia digitale, mentre lo spessore del filo è misurato in 180 (5×36 supporti) sezioni lungo tutta la lunghezza tramite in sistema a lama laser (Fig.4).