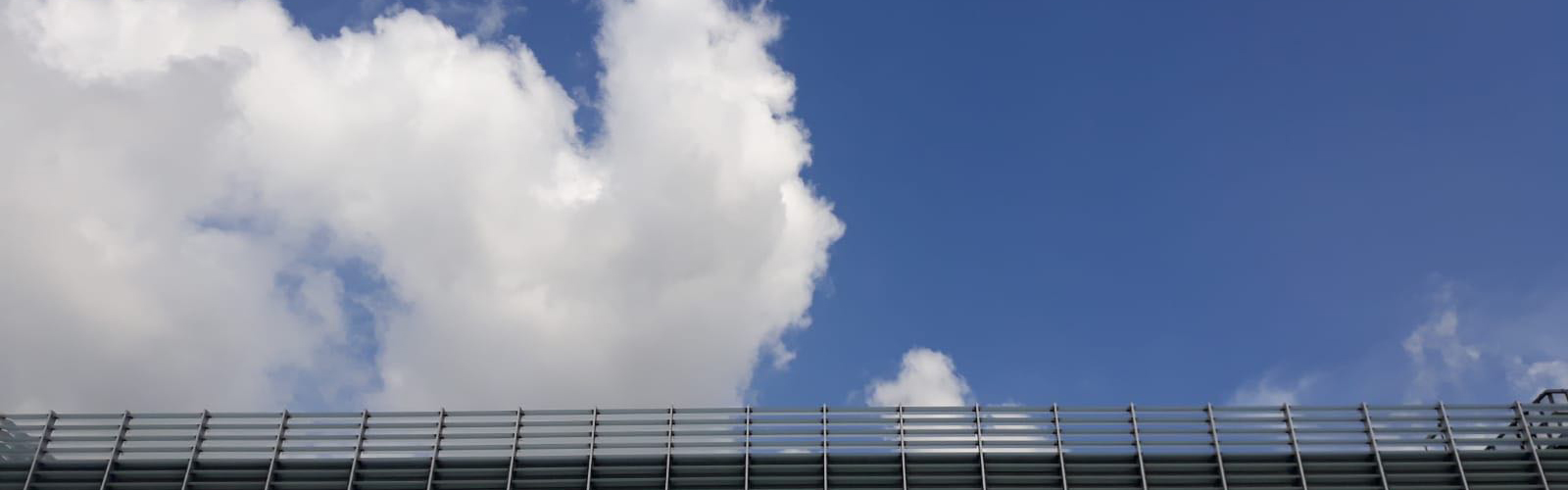
Il primo collettore di scarico per motocicli prodotto tramite tecnologia Laser Metal Deposition
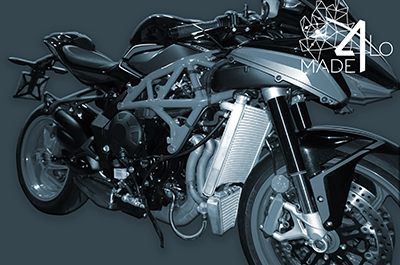
Grande, complesso nella forma e funzionale: i partner di Made4Lo raggiungono un altro traguardo con un dimostratore funzionante che mostra le capacità della produzione additiva avanzata e dell'assemblaggio all'interno dei processi.
Il progetto Made4Lo – Metal Additive for Lombardy, nasce nel 2017 con l’intento di creare una fabbrica diffusa per lo sviluppo delle tecnologie di produzione additiva dei metalli all’interno del territorio lombardo, costituendo così una rete di aziende e centri di ricerca che condividono le loro competenze. Nel corso degli anni si è creato quindi un nuovo modello di “fabbrica di rete” basato sulla conoscenza diffusa e applicata delle tecnologie di stampa 3D, su processi e infrastrutture condivisi dai diversi soggetti della filiera e su una intensa attività di formazione del personale tecnico.
La partnership coinvolge numerose realtà, fra cui nello specifico due centri di ricerca (Politecnico di Milano e Università di Pavia), ed imprese quali Tenova, BLM, GF Machining Solutions, 3D-NT, GFM, Fubri, Costamp Group e Officine Meccaniche Lafranconi.
Tra tre partner in particolare, Politecnico di Milano, Lafranconi e BLM, si è creata una collaborazione per il redesign e produzione di un collettore di scarico per una motocicletta a tre cilindri tramite tecnologia Laser Metal Deposition (LMD). L’attività di ricerca è stata condotta all’interno del laboratorio AddMeLab tramite cella di deposizione BLM Additube. Sviluppata in collaborazione col Politecnico, la cella è costituita da due unità robotizzate: un braccio antropomorfo a 6 assi sul quale è montato il sistema di deposizione e una tavola roto-basculante. Insieme offrono piena libertà di lavoro e gestione di geometrie altamente complesse e di grandi dimensioni.
All’interno del progetto sono state affrontate diverse tematiche relative al Design for Additive Manufacturing (DfAM) e a nuove strategie di deposizione e produzione, oltre allo sviluppo e implementazione del software CAM in ambiente Siemens NX. Il lavoro di integrazione software svolto in collaborazione con Team3D e CNR-Stiima ha permesso di affrontare le sfide che la complessità del prodotto richiedeva.
È stato infatti possibile depositare su componenti appartenenti al modello di serie dello scarico come le flange di connessione al motore; sono state sviluppate strategie per la costruzione in parallelo di più elementi tubolari a parete sottile, evitando collisioni e progettando il loro punto di giunzione garantendo una tenuta a gas e resistenza meccanica. All’interno del processo di stampa, durato in totale 14 ore, è stato inserito il filtro catalizzatore ed è stato saldato utilizzando lo stesso setup di deposizione. Le geometrie del design finale sono il risultato del lavoro del designer Andrea Valensin.
Successivamente alla fase di produzione sono state eseguite sia lavorazioni meccaniche sia di saldatura per l’inserimento di alcuni componenti utili all’assemblaggio col resto del motore e del sistema di scarico.
Il prototipo è stato infine montato e testato su banco prova; i risultati di coppia e potenza ottenuti sono stati comparati con quelli del modello di serie. Grazie alle conoscenze di processo del Politecnico e all’esperienza nel settore di LAFRANCONI è stato possibile ottenere un prototipo con prestazioni paragonabili al modello di serie, dimostrando il potenziale della tecnologia LMD e la validità dei valori di fabbrica di rete promossi dal progetto Made4Lo.