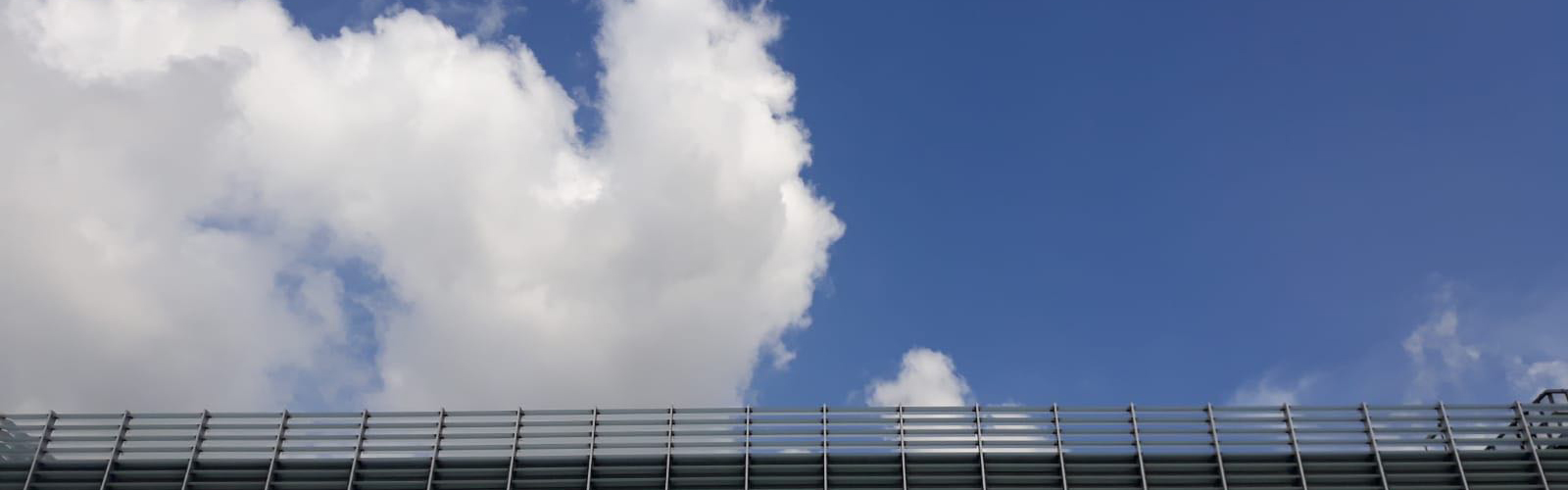
Laboratorio Interdipartimentale LiDuP: strutture leggere e prestazioni di durabilità

Il Laboratorio LiDuP (Lightweight structure and Durability Performance Lab) del Politecnico di Milano è in grado di fornire un servizio essenziale nella progettazione di prodotti ‘lightweight’ che, al giorno d’oggi, sono parte integrante della costruzione di un veicolo (sia terrestre sia aeronautico). Il laboratorio è stato lanciato dalla nostra Università nel maggio 2017 e, al momento, vede la collaborazione di tre Dipartimenti (Dipartimento di Meccanica, Chimica, Dipartimento di Materiali e Ingegneria Chimica “Giulio Natta”, Dipartimento di Ingegneria Civile e Ambientale). È in grado di fornire un supporto sia teorico sia sperimentale al settore dell’industria, nell’ambito dell’Industria 4.0.
Per sviluppare concetti innovativi di ‘lightweight construction’, sono richieste strumentazioni specifiche per eseguire prove sperimentali e caratterizzare materiali e componenti. Il Laboratorio LiDuP fornisce un servizio d’eccellenza nello sviluppo di prodotti “lightweight” di medie dimensioni grazie a un completo supporto sperimentale e teorico. Il Laboratorio, inoltre, offre strutture per la preparazione di materiali con struttura in grafene o nanotubi di carbonio: la messa a punto dei relativi parametri di solubilità permette di raggiungere una dispersione e un’interazione stretta con matrici liquide e polimeriche. Da un punto di vista scientifico, uno dei Comitati di valutazione del Consiglio di Ricerca Europeo (PE8_13) fa riferimento a ”lightweight construction”.
Supporto sperimentale: il Laboratorio LiDuP permette di eseguire prove sperimentali su componenti soggetti a stress termico, ambientale (umidità), chimico (raggi UV, ozono) e meccanico pluriassiale in una scala afferente a componenti di medie dimensioni. Nello specifico, il laboratorio fornisce la possibilità sia di sviluppare prodotti ed eseguire prove sperimentali su componenti complessi (ad esempio, bussole elastiche, bracci di sospensioni di veicoli, componenti di strutture civili, vari tipi di oggetti di consumo, ecc.), sia di effettuare valutazioni sperimentali di variazione delle caratteristiche fisiche durante il ciclo di vita dei componenti (affidabilità nel tempo ). Il laboratorio, inoltre, vanta strutture dedicate alla funzionalizzazione di forme allotropiche di carbonio, tra cui grafene e nanotubi di carbonio. I seguenti sistemi disponibili permettono di impostare set-up ad hoc (Statico, a Fatica, Termico, Combinato e Durata) basati su:
- Dimensioni dei componenti fino a 2000 x 800 x 1000 mm (o superiori con adeguate impostazioni di prova);
- Temperatura e controllo dell’umidità (da -70 a +180 °C, dal 5% al 90% RH);
- Lampade UV (su richiesta);
- Generatori di Ozono (su richiesta);
- 4 o più attuatori idraulici per carico simultaneo (carico dinamico fino a 170 kN, frequenza dipendente da configurazioni di prova).
Il laboratorio LiDuP vanta set-up unici sul territorio nazionale (e, come nella configurazione proposta, nella Figura 1, in Europa)
Supporto teorico: Il laboratorio fornisce la progettazione e la valutazione di prove sperimentali basati su software proprietari e commerciali appartenenti a: meccanica del continuo e meccanica dei materiai, dinamica dei sistemi multi-corpo, teoria dell’ottimizzazione, dinamica dei veicoli. Inoltre, affronta tematiche nell’ambito della chimica e dei materiali, trattati sia a livello macro sia su scala nanometrica. Il laboratorio è stato coinvolto nell’analisi di un braccio di una sospensione in plastica (ibrido) in campo automobilistico, Figura 2. In questo progetto (Progetto SOLE, SOLE2 FESR EU/Regione Lombardia) è stata studiata a livello teorico e sperimentale la progettazione alleggerita di un braccio di una sospensione McPherson.
La struttura ibrida del braccio è stata realizzata attraverso l’uso di PA66 rinforzato con fibre corte in unione con delle lamiere di Alluminio 6061 T6 usate come rinforzo nei punti critici della struttura, Figura 2. Le proprietà strutturali sono adeguatamente supportate dalla parte costruita in PA66 con un rinforzo di fibra di vetro, mentre lo strato di alluminio evita la separazione dei componenti in caso di rottura.
La progettazione del braccio, in conformità con i paradigmi dell’Industria 4.0, è avvenuta interamente attraverso un processo digitale, che è stato utilizzato anche per la costruzione. Il materiale e l’incollaggio sono stati interamente caratterizzati da test sperimentali su prototipi semplificati. Il prototipo finale è stato quindi provato in una camera climatica per valutarne le prestazioni. È stata applicata una forza longitudinale quasi-statica da un attuatore idraulico, in parallelo alla misurazione della deformazione della struttura, Figura 3.