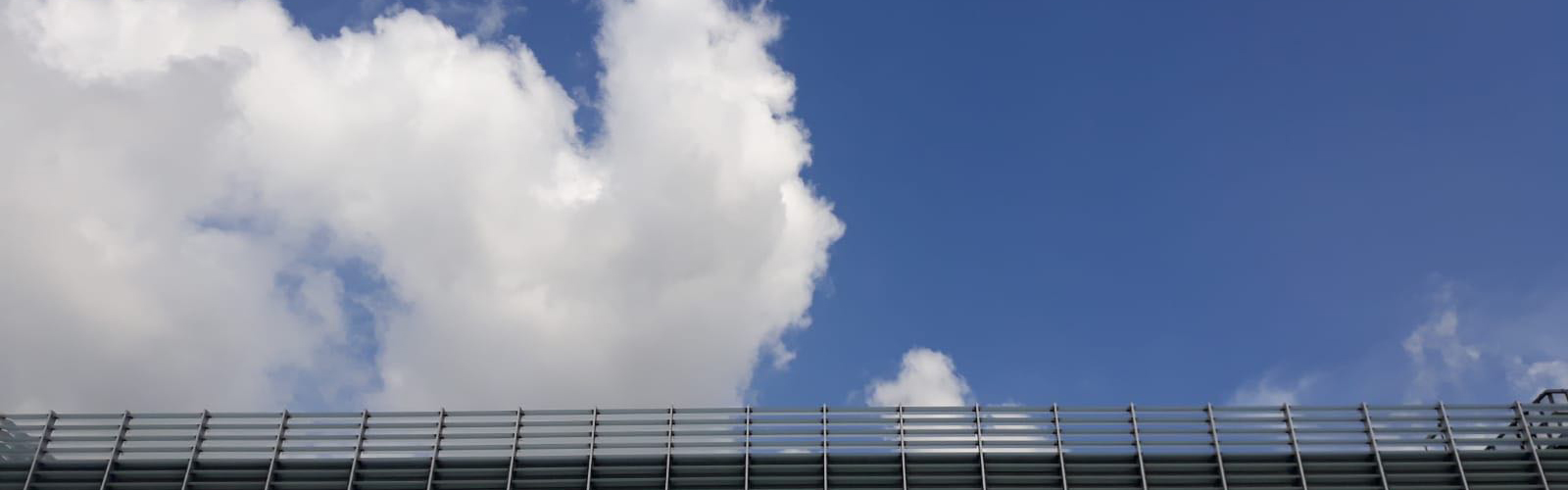
Progetto LIS4.0: intervista a Barbara Previtali, responsabile del WP1

Di cosa si occupa il WP1 nell'ambito del LIS4.0? Quali sono le principali sfide che affronta?
Il WP1- Smart metal additive manufacturing per strutture 4D funzionalizzate è il primo dei WP del progetto LIS4.0 (LIghtweight and Smart structures for industry 4.0). Nel WP1 il tema generale del progetto LIS4.0, ovvero lo studio di strutture lightweight e smart, integrate, progettate, realizzate e sensorizzate usando i paradigmi di I4.0 nel settore della mobilità sostenibile è dedicato ai processi Additive Manufacturing. L'Additive Manufacturing (AM) difatti abilita una nuova progettazione, che integrando materiali leggeri, con funzionalità ottimizzate e prestazioni elevate, assicurate anche dall'assenza di difetti attraverso il monitoraggio di processo, consente la realizzazione di componenti non solo più performanti ma anche più sostenibili per quanto riguarda impatto ambientale e consumo di risorse.
Le sfide del WP1, pertanto, riguardano tutti gli steps che portano a questa nuova famiglia di prodotti leggeri, funzionalizzati e smart realizzati attraverso AM: progettazione, materiali e loro prestazioni, processi zero-defect grazie al monitoraggio e qualifica.
Quale è lo stato delle tecniche di progettazione collegate all'AM?
L’AM è un insieme di processi e tecnologie nuove che liberano i progettisti di prodotto da moltissimi dei vincoli dettati dai processi manifatturieri più tradizionali. Per fare un esempio molto semplificato pensiamo ad un componente del telaio di un'auto elettrica. Pensiamo di volerlo progettare e poi realizzare a spessore variabile, ovvero molto robusto dove deve resistere a carichi sia statici, sia dinamici, sia a urto e più sottile o leggero dove deve solo sostenere la copertura della carrozzeria. Realizzare questo componente mediante processi tradizionali richiede o lo stampaggio di più parti di diverso spessore, per poi saldarle, o la fusione in stampi molto complessi. Al contrario con processi AM può essere ottenuto di singolo pezzo a spessore variabile o ancor meglio densità variabile, senza che questa libertà di progettazione a spessore variabile abbia un impatto sui costi di produzione.
Alla domanda dovrei rispondere con franchezza sottolineando come le tecniche di progettazione siano mature da lungo tempo, più di quanto lo siano i processi AM. Si prendano ad esempio tutti gli strumenti di ottimizzazione topologica. Non sono strumenti recenti, sono strumenti oggi resi molto potenti dalle possibilità e dai gradi di libertà offerti dalla tecnologia AM. Tuttavia, abbiamo bisogno che il progettista conosca e disponga di una nuova metrica ed ontologia che gli consenta di progettare forme, funzioni, estetiche nuove amplificando le potenzialità date dall'AM ma senza cadere nelle trappole dei limiti che anche le tecnologie AM hanno. Per questo nel WP1 studiamo uno strumento di design for AM, che consenta la progettazione di prodotto ottenibile mediate AM e che anticipi ed includa nel processo di progettazione le regole per la produzione AM.
Ci sono dei materiali che state studiando e che giudicate promettenti per specifiche applicazioni?
Una parte fondamentale del WP1 è dedicata ai nuovi materiali e alle nuove polveri. Non posso raccontare qui per ragioni di spazio tutto ciò che si sta indagando. Mi limiterò a fare alcuni esempi. Per cominciare, stiamo studiando materiali a transizione di fase che applicati alla realizzazione di scambiatori di calore permettono di asportare calore non solo grazie ai tradizionali meccanismi di conduzione e convezione allo stato solido, ma anche sfruttando la transizione solido/liquido di alcune fasi in essi presenti. L'aggiunta di questo meccanismo ulteriore di asportazione del calore rende gli scambiatori più performanti e consente di ridurne le dimensioni con evidenti vantaggi in termini di alleggerimento del componente. Come secondo esempio possiamo considerare l’applicazione delle tecnologie additive ai materiali piezoceramici. Per questa famiglia di materiali il processo di stampa più adatto è il Binder Jetting, e nel progetto si è partiti dalla sintesi di polveri di diversi materiali e si è arrivati alla realizzazione di forme difficilmente ottenibili con i processi tradizionali a meno di ingenti spese nella realizzazione degli stampi (Fig.1 - Esempio).
Considerando più in generale l’ampia famiglia delle tecnologie additive, le polveri di partenza sono uno dei principali responsabili della buona realizzazione del processo di stampa. Per questa ragione, nel progetto, ampio spazio è riservato alla analisi delle proprietà della polvere che ne caratterizzano la processabilità. Sono state proposte alcune composizioni appositamente progettate per la stampa additiva e si è valutato anche come e in che quantità sia possibile riciclare parte della polvere coinvolta nel processo di stampa, ma non fusa, così da avere un processo maggiormente sostenibile ed ecologico.
Quali sono i processi AM innovativi che state sperimentando? E con quali risultati?
Grazie a LIS4.0 il Dipartimento ha arricchito la sua dotazione hardware di due nuovi sistemi di stampa. Il primo sistema, Studio System+ di Desktop Metal (Fig.2 - Fase di stampa BMD di feedstock metallico mediante testa di estrusione (componente: manifold, materiale: 316L, ugello di estrusione: 0.4mm)), è basato sul principio, sviluppato in collaborazione col Massachusetts Institute of Technology, della stampa mediante estrusione di feedstock metallico (Bound Metal Deposition, BMD). La deposizione della geometria 3D sfrutta la presenza nel composto metallico del legante polimerico, mentre la densificazione del metallo avviene mediante successiva sinterizzazione in forno. Grazie a questo è possibile ottenere componenti in materiali difficili da stampare mediante tecniche a fusione, come il rame o gli acciai per utensili (un esempio di stampa in rame è mostrato in Fig.3 - Parti sinterizzate in rame puro ottenute mediante tecnica BMD (componenti: filtri con riempimento a lattice tipo diamante, materiale: rame puro, ugello di estrusione: 0.25mm)).
Il secondo sistema è una stampante SLM (Selective Laser Melting), principio sicuramente più consolidato ma con funzionalità uniche e non commerciali. Si tratta difatti di un sistema di stampa aperto, ovvero che consente di testare soluzioni innovative, come l'utilizzo di una sorgente laser modulabile nel tempo, ovvero che può lavorare in modalità sia pulsata sia continua, o modulabile nello spazio, ovvero che varia la distribuzione di potenza da gaussiana a multimodo. È possibile poi strumentare il sistema, integrando diversi sensori di processo (termocamera off-axis, camera NIR – Near InfraRed - coassiale, sensore di vibrazione della racla, etc.) e coordinare l'azione dei sensori con la movimentazione del fascio laser e della racla. In questo modo si abilita il sensing, il monitoraggio ed eventualmente il controllo durante la stampa. Un esempio di risultato ottenuto con il sistema SLM open è la stampa di micro-lattici in Zn puro in Figura 4 (Strutture lattice in lega di Zinco stampati mediante tecnologia SLM con strategie di scansione innovative (spessore delle strutture inferiore a 0,2 mm)), una lega difficile da processare laser vista la sua bassa temperatura di vaporizzazione, ottenuta attraverso il controllo del singolo impulso laser.
L'intelligenza artificiale è uno strumento ormai pervasivo; come trova applicazione nell'AM?
Grazie al paradigma di produzione strato su strato, i processi AM permettono un livello completamente nuovo di accesso a misure in tempo reale durante la realizzazione di ogni singolo strato del prodotto. È infatti possibile acquisire grandi quantità di dati attraverso una varietà di sensori, tra cui fotocamere e termocamere, per tutta la durata del processo. È qui che l’intelligenza artificiale gioca un ruolo chiave, in quanto permette di elaborare questa grande mole di dati, complessi e variegati, permettendo al sistema di identificare, in modo automatico e tempestivo, condizioni anomale e instabilità di processo, anticipando il riconoscimento di difetti nella parte in produzione. Permette inoltre di intervenire, quando possibile, con azioni correttive e adattative, per ridurre gli scarti e migliorare qualità e produttività degli impianti.
Lo studio di nuove soluzioni di intelligenza artificiale e analisi di dati complessi è uno dei temi di ricerca del progetto LIS4.0, che trova applicazione in processi AM a letto di polvere e basati su estrusione di materiale.
Avete in previsione lo sviluppo di prototipi che rappresentino risultati dei vostri studi, specialmente nel settore automotive, argomento principale di LIS4.0?
Uno dei prototipi che stiamo studiando nel WP1 è la camicia di raffreddamento per un motore elettrico in-wheel della vettura sviluppata dal team DynamiS per la Formula SAE. Questo componente è stato progettato per essere prodotto in lega di alluminio tramite SLM ed è caratterizzato dall’utilizzo di strutture “lattice” per migliorare le caratteristiche di scambio termico. Allo stato attuale della ricerca le strutture TPMS (triply periodic minimal surface), ed in particolare la struttura giroide, sembrano offrire le migliori prestazioni in base ai risultati ottenuti con analisi numeriche di fluidodinamica (CFD). Tramite il sistema SLM open di LIS4.0 poi si è ottimizzato il processo SLM in una modalità di stampa innovativa, che permette l'ottenimento di pareti molto sottili e di geometrie a sbalzo che non necessitano di supporti. In questo modo le geometrie ottime delle strutture giroidi risultato della simulazione CFD sono state realizzate e testate (un’immagine della struttura soggetta ai test è mostrata in Figura 5 - Esempio di struttura giroide stampata SLM in alluminio sottoposta a test meccanico).