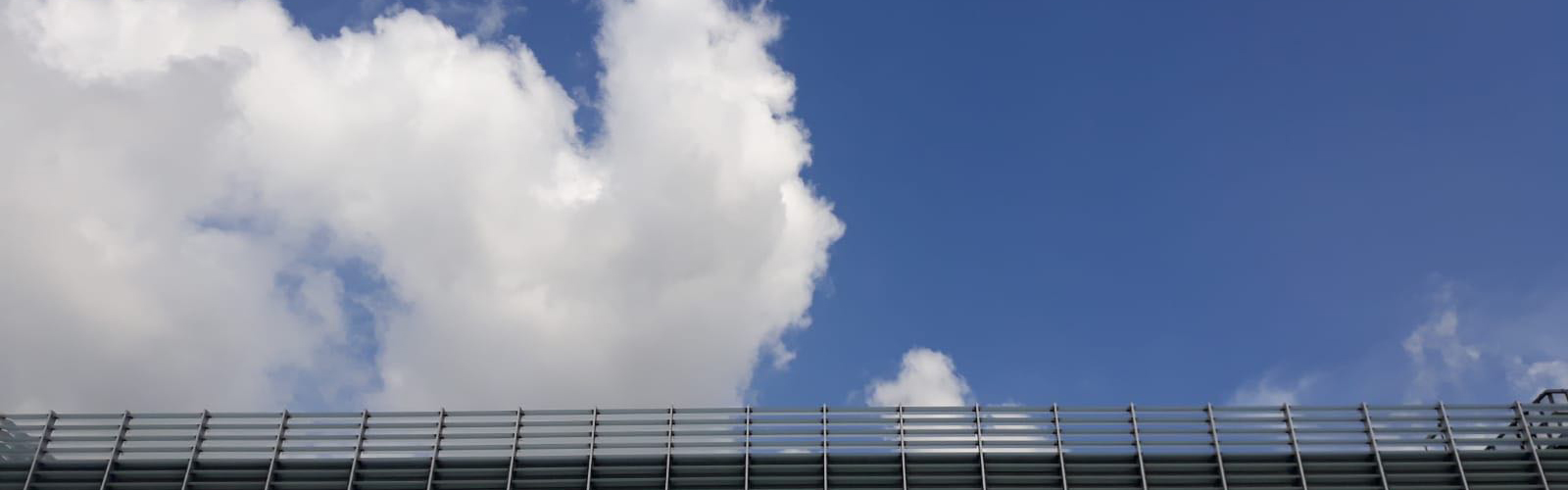
Progetto LIS4.0: intervista a Francesco Braghin, responsabile del WP2
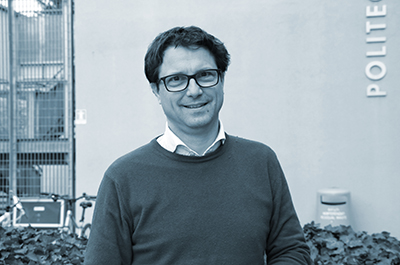
Di cosa si occupa il WP2 nell’ambito del LIS4.0? Quali sono le principali sfide che affronta?
Il WP2 di LIS4.0 si è occupato della progettazione e realizzazione di estrusori sensorizzati in grado di "bagnare" la fibra lunga di carbonio (o di vetro) con la matrice termoplastica in modo ottimale nonché di depositare la fibra sul manufatto con pressione e temperatura ottimali per massimizzare l’adesione e quindi le prestazioni meccaniche del pezzo finito. Le sfide per la realizzazione sono molteplici: se la fibra non viene "bagnata" correttamente, le prestazioni del manufatto finale saranno molto inferiori di quelle attese; se non riesco a depositare la fibra con la pressione e temperatura ottimale, questa non aderirà allo strato sottostante; se la velocità di estrusione non è legata alla velocità di avanzamento dell'estrusore, non riuscirò a realizzare componenti della forma voluta ma rischio di lasciare grinze nel manufatto o addirittura di spezzare la fibra che sto depositando.
Quali sono le soluzioni innovative esplorate per le strutture in materiale in composito, sia in termini di progettazione che di gestione dell’intero ciclo di vita dei prodotti?
Per risolvere le sfide sopra descritte, è necessario adottare un approccio integrato: non posso pensare all'estrusore senza tenere conto del materiale che sto estrudendo o del manufatto sul quale sto depositando la fibra e non posso pensare di ottenere parametri tecnologici ottimali di stampa se non ottimizzo anche i profili di velocità e le traiettorie lungo le quali muovo l'estrusore. Si è pertanto adottato un approccio olistico che tenga conto del materiale di partenza, del processo tecnologico di estrusione - poltrusione nonché della struttura meccanica e del controllo di estrusore e braccio robotico che movimenta l'estrusore stesso.
Inoltre, tenendo conto che la fibra lunga "stampata" può essere anche una fibra di vetro e che quindi può essere utilizzata per monitorare il manufatto prodotto (ad esempio mediante tecnologia Optical Backscatter Reflectometer o semplicemente OBR), non solo si è stampata una struttura 3D in carbonio ma si è anche integrato un sistema di monitoraggio distribuito in grado di tenere sotto controllo le sollecitazioni (meccaniche e termiche) cui il componente è sottoposto durante la sua vita utile per migliorare la sicurezza e l'affidabilità del pezzo stesso.
Quali applicazioni possono essere abilitate dall’integrazione di sensori e dallo sviluppo di materiali con proprietà self-healing?
Il monitoraggio di componenti (sia critici che non) riveste oggi un interesse sempre maggiore in quanto permette di cambiare la filosofia di manutenzione: da programmata a predittiva. Per componenti mission critical questo cambio di prospettiva è di fondamentale importanza: mentre oggi per garantire i necessari standard di sicurezza si è costretti a frequenti ispezioni non distruttive che richiedono tempo e denaro, con un sistema di monitoraggio integrato nel componente stesso si riuscirebbe a prevedere la vita rimanente del pezzo e quindi ad intervenire solo quando necessario.
Quali sviluppi prototipali sono stati effettuati nel BAAM 3D moldless?
Per ora ci siamo limitati a realizzare provini semplici che ci hanno permesso di verificare la bontà del progetto e del processo implementato. La prospettiva rimane quella di provare a realizzare componenti meccanici per applicazioni automotive.