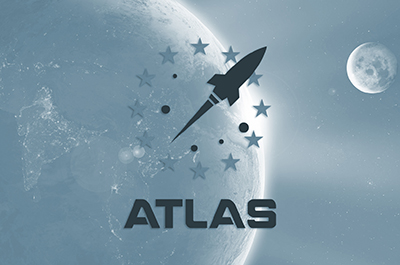
Within the programme Horizon2020-SPACE, the European Commission issued 3 million euros to fund the ATLAS project, coordinated by the Department of Mechanical Engineering of Politecnico di Milano (Prof. Mario Guagliano). “ATLAS” - Advanced Design of High Entropy Alloys Based Materials for Space Propulsion (GA n. 101004172) – aims at developing new materials capable of ensuring high-performing properties in extreme environmental conditions, allowing a considerable step forward in designing and construction of space propulsion systems. In fact, one of the major problems linked to these missions is to create systems able to perform without yielding in extreme environments with sudden temperature variations, rising from below zero to more than hundreds degrees. In particular, the space propulsion systems work under severe stress conditions and need adequate design to resist these conditions, which doesn’t necessarily meet the requirements to maximise weight reduction. The solution to this problem is to develop ad hoc materials that combine all requested properties and maintain them in extreme environments, namely the ones typical of space exploration missions.
The ATLAS project aims at solving such problems. Its objective is to develop new materials made of High Entropy Alloys (HEA) capable of enduring harsh conditions by combining low density, high resilience, high ductility, high oxidation resistance, good mechanical properties under stress and creep.
HEAs are part of a relatively new class of materials aimed at replacing superalloys in harsh applications, thanks to their higher-performing properties. However, they haven’t been widely applied yet because of some unsolved issues. Finding a solution is precisely what the ATLAS team ambitiously aims to do and, in so doing, also wiping out all reasons still limiting the usage of these materials.
By the multidisciplinary approach taken thanks to the involved partners complementing one-another, the team wants to design and produce high entropy alloys and composite materials with a HEA matrix and ceramic materials as reinforcement, allowing to optimize the requested properties for their application into the combustion chambers of space propulsion systems.
The planned steps to reach such ambitious results are: defining and classifying the properties of interest; designing HEAs with multi-scales and multidisciplinary approaches; defining hybrid/composite solutions by combining HEAs with ceramic materials and/or ceramic matrix composites to create functional, light and high-temperature resistant materials. Using these materials for coatings and manufactory of components requires two different and complementary additive manufacturing techniques: Powder Bed Fusion (PBD), a thermal nature process, and Cold Spay, a dynamic process.
Other than coordinating the project, DMEC focuses on cold spray applications. This process exploits the phenomenon of adhesion of solid powders obtained by accelerating the powder spray rate to a supersonic speed, higher than its critical value. Overcoming this limit activates the phenomenon because of the severe plastic deformations occurring and the high strain rate, building through more layers of superficial coatings and 3D pieces. It is indeed a highly-ambitious challenge because the attempts to use cold spray on HAS are very few, and nobody has yet tried on HEA composites.
Besides, it will be of great interest to follow the definition of the optimal parameters and results, defining the properties the new materials will show, seeing their application on a space propulsion system by one of our partners, and confronting the obtained results with other technologies being studied.
Other than Politecnico di Milano, the consortium includes the Deutsches Zentrum für Luft und Raumfahrt (DLR), a well-known German Aerospace Research Centre, the University of Derby (UK), and a few highly-specialised technical SMEs: Arceon (NL), Dawn Aerospace (NL), Questek (SE), Tisics (UK). YourscienceBC (UK) will handle the dissemination of the results.