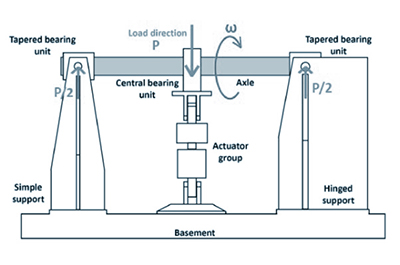
Railway axles are critical components, and their design assessment procedure, as well as the maintenance program, require special attention. The design route must consider the deterioration of the axles during service that can be promoted by different source of surface damage: ballast impacts, pitting from corrosion and surface scars in press-fits. All these types of damages can lead to fatigue crack growth under a sufficient level of local cyclic stresses.
Establishing a quantitative procedure for determining residual axle lifetimes is of fundamental importance, and it is still the subject of scientific studies. Experimental investigation of the fatigue crack growth behavior of a full-scale railway axles is fundamental in order to investigate on the phenomena (i.e. residual life) and validate related models. For these reasons a Dynamic test bench for full scale railway axle has been developed in DMEC lab.
The full-scale axle fatigue test bench consists of one central bearing unit connected to an actuator that applies a vertical load on the specimen, with 250 kN load capacity, and two supports carrying the axle through tapered bearing units. The specimen is rotated using an electric motor to generate rotating bending fatigue. Three-point rotating bending load on a full-scale railway axle specimen test can be performed using this bench. The test bench is equipped with a microscope for taking picture of the axle surface and a cell for corrosion-fatigue tests.
The type of test that can be carried out:
- fatigue tests under constant and variable amplitude loads;
- crack propagation tests under constant and variable amplitude loads;
- corrosion-fatigue tests.