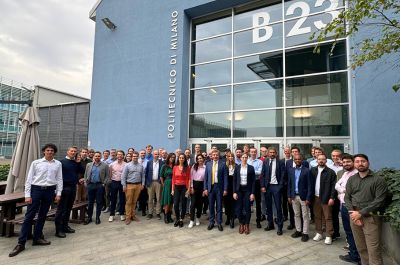
The European manufacturing industry is entering a transformative phase, driven by the urgent need for more sustainable, circular economy practices. Among these, remanufacturing is a particularly valuable solution, offering a significant reduction in material consumption (up to 80%) and CO2 emissions (up to 90%) when compared to traditional manufacturing. However, modern high-value products are becoming increasingly complex and "smart," incorporating sensors and electronics. This complexity introduces new challenges to remanufacturing processes.
The rEUman project, which had its kick-off meeting on 1st and 2nd of October, is dedicated to addressing these challenges with innovative solutions.
Coordinated by Professor Marcello Colledani from the Department of Mechanical Engineering at Politecnico di Milano, rEUman brings together 20 partners from across 9 EU Member States, Turkiye, and the UK, with the involvement of different research groups of our Department and the Department of Management. The project aims to boost remanufacturing by developing a digitally enhanced and human-centric approach, creating a more flexible, sustainable, and robust system that expands remanufacturing from simple components to more complex, high-added-value products.
The project’s overarching goal is to tackle the limitations currently holding back the remanufacturing sector. These include challenges such as manual disassembly, poor traceability, and a lack of automation. By focusing on these gaps, rEUman seeks to increase the adoption of remanufacturing processes across industries like automotive, household appliances, and optoelectronics. This transformation will help the European manufacturing sector reduce dependency on raw material extraction, while creating new knowledge-intensive jobs and skills.
rEUman will introduce several groundbreaking innovations to achieve these goals. New inspection technologies will increase the traceability of post-use products, ensuring that recovered parts meet the highest quality standards, ultimately enhancing customer confidence. Furthermore, hybrid automation and human-empowerment solutions will make manual tasks safer and more efficient, improving working conditions and boosting productivity. The project will also implement advanced regeneration techniques, such as visual servo-based robotics and cold-spray technology, allowing for more accurate and high-quality remanufacturing of electronic and mechanical components.
A critical part of rEUman’s strategy is the development of a Digital Product Passport (DPP). This will enable better data management and traceability across the entire remanufacturing value chain, allowing manufacturers and remanufacturers to collaborate more effectively. Built on open-source technologies, the DPP will ensure transparency and streamline processes across multiple sectors.
These innovations will be validated through three industrial pilots across key sectors and five demo cases, showcasing the flexibility and scalability of the rEUman approach. With this validation, the project will demonstrate how its solutions can be adapted to different industries and products, making remanufacturing a viable option for more complex, high-added-value items.
To ensure the success of these innovations, rEUman is also addressing the skills gap in the remanufacturing sector. By developing training mechanisms and learning resources, the project will prepare the next generation of experts, equipping them with the skills needed to thrive in this evolving industry.